Famille d’alliage
AluminiumType
FonderieDésignation
AA 170.0Élaboration/Traitement
Moule en sableÉtat métallurgique
Brut de couléeN° de fiche
Al-09Nomenclature
La série AA 1xx désigne les alliages d’aluminium non allié, de pureté très élevée. Le AA 170.0 est une désignation normée par l’Aluminium Association. Le « .0 » indique la forme du produit, soit une pièce coulée (alors que « .1 » serait un lingot). Cet alliage AA 170.0 était anciennement l’alliage « 100 » et le « RP-S », aussi appelé « aluminium à rotors ».
Méthode d’élaboration
L’alliage a été conçu à partir de lingots de AA 170.1, et aucun élément d’alliage n’a été ajouté. Il a été coulé dans un moule au sable aggloméré chimiquement en forme d’éprouvette de traction de 3/8 pouce de diamètre.
État métallurgique
L’état métallurgique est brut de coulée en moule au sable. C’est un état normé du point de vue des propriétés mécaniques.
Remarques sur la composition chimique
Le ratio « teneur en fer/teneur en silicium » est contrôlé à 1,5 pour améliorer la coulabilité de l’alliage par la formation d’un eutectique Fe-Si.
Remarques sur la microstructure
La matrice est composée d’aluminium primaire « α » à 100 %. Sans attaque chimique, quelques défauts sont visibles, tels que des microretassures et des oxydes. L’attaque au HF et au Keller permet d’observer les impuretés aux joints de grains. Il est cependant impossible de différencier les impuretés au microscope optique. Selon la « méthode des interceptions » de la norme ASTM E112, la taille des grains correspond à un indice « G » de 2, ce qui donne une dimension moyenne de 179,6 µm.
Les composés de cet alliage qui ont été observés au microscope électronique à balayage (MEB) sont le FeAl6, les composés de Al-Fe-Si (probablement du Fe3SiAl12) et ceux de Fe-Al-Ni.
L’attaque électrolytique au Barker avec lumière polarisée et filtre tintant permet de bien observer deux types de grains. Au centre, les grains sont de formes basaltiques, ce qui indique que le refroidissement est dirigé du centre vers l’extérieur. Les grains basaltiques se forment lorsque l’extraction de chaleur est dirigée, mais faible (gradient thermique bas), ce qui laisse le temps aux dendrites de croître perpendiculairement aux parois du moule.
Près de la surface du moule, les grains sont de formes équiaxes (arrondis et orientés au hasard), signe d’un refroidissement rapide et d’une germination sur la paroi.
Quelques « rosettes » sont également présentes, facilement identifiables par leur profil convexe, allant même jusqu’à une structure parfaitement circulaire. Les « rosettes » se forment durant la solidification lorsque du métal liquide, riche en éléments d’alliage, est emprisonné entre les premières dendrites solidifiées.
Remarques sur les propriétés mécaniques
Cet alliage a des propriétés mécaniques se classant dans la gamme inférieure de tous les alliages d’aluminium de fonderie. Par contre, sa ductilité et sa conductivité thermique et électrique sont exceptionnelles.
Préparation métallographique
- Meulage sur papier 320 grains (2 min.);
- Polissage avec particules diamantées en suspension : MD-Largo 6 µm (5 min.), MD-Mol 3 µm (6 min.) (optionnelle), MD-Mol 1 µm (5 min.), MD-CHEM avec OP-U Non-Dry (1 min.) (finition).
Applications possibles
L’alliage de fonderie AA 170 est principalement utilisé pour fabriquer des rotors (de diamètre inférieur à 15 cm) servant dans de petits moteurs électriques.
Provenance/Fabrication
Les lingots ayant servi à l’élaboration proviennent de AIM Solder, Montréal, Québec, Canada.
Contributeur(s)
Famille d’alliage
AluminiumType
FonderieDésignation
AA 170.0Élaboration/Traitement
Moule en sableÉtat métallurgique
Brut de couléeN° de fiche
Al-09Tableaux des propriétés
Valeurs mesurées | Valeurs normées * | |
---|---|---|
% Si |
0,03 | * |
% Mn |
0,001 | 0,025 max. |
% Al |
99,88 | 99,7 |
% Ni |
0,01 | 0,03 max. |
% Cr |
0,0006 | 0,025 max. |
% Fe |
0,043 | * |
% Ti |
0,0035 | 0,025 max. |
% V |
0,012 | 0,025 max. |
% Zn |
0,003 | 0,05 max. |
* Le ratio Fe/Si est de 1,5 minimum.
Valeurs mesurées | Valeurs typiques * | |
---|---|---|
Dureté (HB) |
14 | 17 |
Rm (MPa) |
61 | 37,6 |
Re (MPa) |
35 | 20,7 |
A (%) |
57,1 | 47 |
E (GPa) |
ND | ND |
* Référence sur la composition chimique
John L. Jorstad and Wayne M. Rasmussen, Aluminium Casting Technology, 2nd Edition, American Foundrymen’s Society, Edited by Donna L.Zalensa, 1993.
* Référence sur les résultats mécaniques
John L. Jorstad and Wayne M. Rasmussen, Aluminium Casting Technology, 2nd Edition , American Foundrymen’s Society, Edited by Donna L.Zalensa, 1993.
Essai de traction
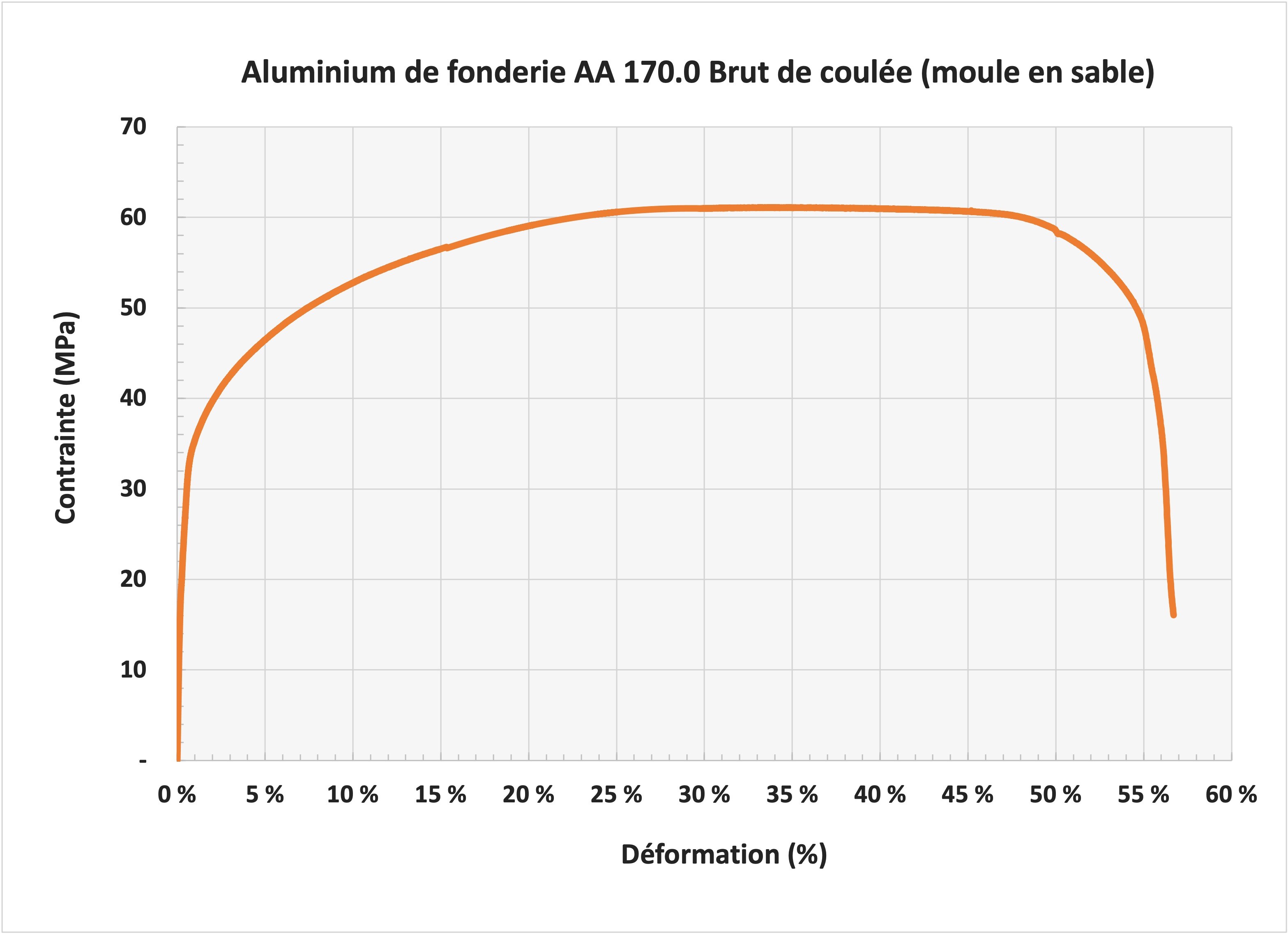