Famille d’alliage
AcierType
OutilDésignation
AISI M2Élaboration/Traitement
ThermiquementÉtat métallurgique
Trempé et double revenu (530 °C)N° de fiche
Ac-46Nomenclature
La désignation « M2 » signifie que c’est un acier de la catégorie « outil » utilisé comme « acier rapide » (ou « HSS », en anglais, pour high speed steel). La lettre « M » évoque la présence élevée de molybdène dans cette sous-catégorie d’acier à outils. Cet alliage est trempable à l’air et possède de hautes teneurs en carbone, en molybdène, en tungstène et en vanadium.
L’acier à outils M2 possède deux variantes commerciales, soit le « régulier carbone » (0,78 %-0,88 %) et le « haut carbone » (0,95 %-1,05 %). Les désignations possibles pour cet acier outil sont B. S.BM 2, DIN 1.3343, HS6-5-2C, SS 2722, SKH51, CW6Mo5Cr4V2 et UNS T11302.
Méthode d’élaboration
Le cycle de trempe et revenu a été appliqué sur un échantillon d’acier AISI M2 préalablement à l’état « sphéroïdisé » (fiche Ac-45). Les paramètres du cycle thermique sont les suivants :
- Montée en température à 250 °C/h jusqu’à une température de 845 °C et maintien de 15 minutes;
- Montée en température à 250 °C/h jusqu’à une température de 1200 °C* et maintien de 5 minutes;
- Trempe à l’air soufflé et retrait de la pièce lorsque 90 °C sont atteints;
- Premier revenu d’adoucissement à 535 °C pendant 2 heures et refroidissement à l’air calme;
- Deuxième revenu d’adoucissement à 515 °C pendant 1 heure et refroidissement à l’air calme.
*Cette température d’austénitisation très élevée à 1200 °C est nécessaire pour solubiliser les carbures de chrome (M23C6), de tungstène (M6C) et de molybdène (M6C). Cette dissolution permet alors de libérer le carbone qui peut alors produire une martensite à haute teneur en carbone. Quant aux carbures de vanadium (VC), très peu seront dissous, même à une température proche du solidus.
État métallurgique
L’état « trempé et revenu » est un état terminal d’une pièce en acier outil M2. Comme l’acier AISI M2 contient du chrome (4 %), du molybdène (5 %), du vanadium (2 %) et du tungstène (6 %), sa trempabilité à l’air est excellente. Un double revenu de détente (à 232 °C ou à 371 °C) ou un double revenu d’adoucissement (de 427 °C à 650 °C) est généralement appliqué. La température du revenu permet d’éliminer les contraintes internes, d’ajuster la dureté de l’outil et/ou de stabiliser les dimensions. Il est aussi apte à la nitruration (gazeuse ou liquide).
Remarques sur la composition chimique
De tous les aciers à outils, les « aciers rapides » sont les plus fortement alliés. La teneur en carbone d’environ 1 % augmente la trempabilité et la dureté de la martensite produite après le cycle de trempe. De même, la haute teneur en carbone permet la formation de carbures de chrome, de vanadium et de tungstène, ce qui augmente significativement la résistance à l’usure. Une teneur en chrome de l’ordre de 4 % sert d’abord à améliorer la trempabilité et est un compromis idéal entre la dureté et la ténacité. Le chrome réduit également l’oxydation durant les traitements thermiques.
Le vanadium est ajouté précisément pour affiner la taille des grains. À une teneur de 2 %, il contribue à la formation de carbures très durs (V4C3) et stables, qui augmentent considérablement la résistance à l’usure et la tenue à chaud.
Le molybdène augmente la dureté après le cycle de trempe par formation de carbures. Combiné au vanadium, il permet aussi une tenue à chaud jusqu’à 540 °C. Le molybdène provoque un durcissement secondaire lors du revenu (500 °C).
Quant au tungstène (6 %), il forme un carbure complexe avec le fer, ce qui contribue de manière significative à augmenter la résistance à l’usure. Le tungstène améliore la dureté à chaud et provoque un durcissement secondaire lors du revenu (500 °C).
Remarques sur la microstructure
Sans attaque chimique, les carbures massifs composés de tungstène, de fer, de chrome et de vanadium sont visibles. L’attaque au picral 4 % fait ressortir une matrice composée de martensite revenue (brunâtre) parsemée de carbures massifs aux contours mieux définis. L’observation au microscope électronique à balayage permet d’identifier deux types de carbures principaux : certains sont plus riches en « tungstène, molybdène et fer » alors que ceux qui sont plus sombres sont plus riches, dans l’ordre, en « vanadium, tungstène et molybdène + nitrures » (voir l’onglet Constituants). Entre 5 % et 8 % de la surface est composée de carbures massifs.
Remarques sur les propriétés mécaniques
Les aciers à outils de cette catégorie possèdent comme principale caractéristique la conservation de leurs propriétés à haute température (500 °C).
L’acier outil M2 est un alliage très disponible sur le marché, mais son coût est élevé en raison de sa composition chimique. La trempe à l’air aide à réduire davantage les distorsions causées par les milieux de trempe plus agressifs comme l’huile ou l’eau. La trempe en bain de sels fondus (500 °C) est aussi employée pour réduire le gradient thermique et réduire le risque de fissuration.
La dureté de la pièce en acier à outils M2 se situe généralement entre 61 HRC et 66 HRC après austénitisation (entre 1080 °C et 1220 °C) suivie d’une trempe à l’air (ou en bain de sels à 500 °C avec trempe interrompue).
Les aciers à outils rapides de type « M » sont plus résistants que les aciers à outils rapides de type « T », mais leur dureté à chaud est légèrement inférieure. La compensation de cette dureté à chaud réduite est partiellement accomplie par l’addition de tungstène et, dans une moindre mesure, de vanadium aux nuances de molybdène. C’est l’une des raisons importantes de la popularité des nuances tungstène-molybdène (comme M2, M3, M4) : elles offrent une bonne dureté à chaud, ce qui est si souhaitable dans les aciers à outils rapides.
Généralement, la série « M » possède une meilleure résistance à l’usure par abrasion que la série « T », elle se déforme moins durant le traitement thermique et elle est aussi moins coûteuse.
Le choix de la température d’austénitisation dépend de l’usage de l’outil. Une température plus basse est privilégiée si l’outil est destiné au travail à froid, et une température plus élevée (1165 °C-1220 °C) est de mise si l’outil est destiné à la coupe (et usinage).
Un double et parfois même un triple revenu d’adoucissement (de 525 °C à 650 °C) est obligatoirement appliqué à la suite de la trempe. Cela est nécessaire pour terminer la transformation de l’austénite retenue en martensite.
Préparation métallographique
- Meulage sur papier 220 grains (2 min.), 320 grains (2 min.), 500 grains (1 min.);
- Polissage avec particules diamantées : MD-Largo 6 µm (5 min.), MD-DAC 3 µm (5 min.), MD-CHEM avec OP-U Non-Dry ou OP-S Non-Dry (1 min.) (finition optionnelle).
Applications possibles
L’acier outil M2 est un alliage très disponible sur le marché, mais son coût est élevé en raison de sa composition chimique (molybdène, vanadium et tungstène).
À l’état sphéroïdisé : état de livraison général et état transitoire pour la mise en forme de l’outil et l’usinage (état métallurgique idéal).
À l’état trempé-revenu : état métallurgique désiré pour la pièce en service. Il est principalement utilisé comme outils de coupe et présente les caractéristiques principales suivantes :
- trempable à l’air ou à huile;
- dureté à chaud jusqu’à 540 °C;
- résistance aux chocs satisfaisante pour l’usage (précautions requises).
L’acier à outils M2 convient à une grande variété d’outils de coupe qui nécessitent des vitesses d’avance modérées. Il fournit une dureté suffisante ainsi qu’une ténacité exceptionnelle pour un « acier rapide ».
Cet acier à outils peut aussi être utilisé pour les applications de travail à froid. Il offre une dureté à chaud et une résistance à l’usure supérieures à celles du D2.
Sa température de revenu élevée (> 540 °C) et sa dureté à chaud en font un excellent substrat pour la plupart des traitements de surface. Par exemple, il est commun que les outils soient recouverts d’une mince couche de nitrure de titane, de carbure de titane et de nombreux autres revêtements par une technique de dépôt physique en phase vapeur pour améliorer leurs performances et prolonger leur durée de vie.
Applications typiques : outils de coupes tels forets, alésoirs, fraises, broches, tarauds, outils pour tours ou fraiseuses, scies à bois, scies à métal, lames de cisaille et cisailles rotatives, outils de formage tels filières d’étirage, matrices de découpage, matrices diverses pour le travail à froid ou le travail à chaud, rouleaux de laminage à froid, matrices de forgeage à froid, matriçage à froid.
Provenance/Fabrication
La barre de 1 pouce de diamètre est distribuée par Precision Marshall Steel Company, Pennsylvanie, États-Unis.
Contributeur(s)
Famille d’alliage
AcierType
OutilDésignation
AISI M2Élaboration/Traitement
ThermiquementÉtat métallurgique
Trempé et double revenu (530 °C)N° de fiche
Ac-46Tableaux des propriétés
Valeurs mesurées | Valeurs normées * | |
---|---|---|
% C |
0,86 | 0,78-0,88 |
% Si |
0,34 | 0,20-0,45 |
% Co |
0,19 | |
% Mn |
0,27 | 0,15-0,40 |
% P |
0,019 | 0,030 max. |
% S |
0,012 | 0,030max |
% Cr | 4,0 | 3,75-4,50 |
% Mo | 4,86 | 4,50-5,50 |
% W | 6,15 | 5,50-6,75 |
% V | 1,85 | 1,75-2,20 |
Valeurs mesurées | Valeurs normées ou typiques * | |
---|---|---|
Dureté (HRC) |
63 | 64 min.* |
Rm (MPa) | 1511** | 2150 |
Re (MPa) | 1490 | ND |
A (%) |
< 1 | ND |
E | 202 | 200 |
* Seule la dureté maximale est normée par l’ASTM A600. La dureté de 64 HRC est le minimum après un double revenu de 2 heures à 552 °C.
** L’éprouvette de traction s’est rompue prématurément.
* Référence sur la composition chimique
Norme ASTM A600-92a (Reapproved 1999)
* Référence sur les résultats mécaniques
https://www.makeitfrom.com/material-properties/Hardened-M2-Tool-Steel et norme ASTM A600-92a pour la dureté
Essai de traction
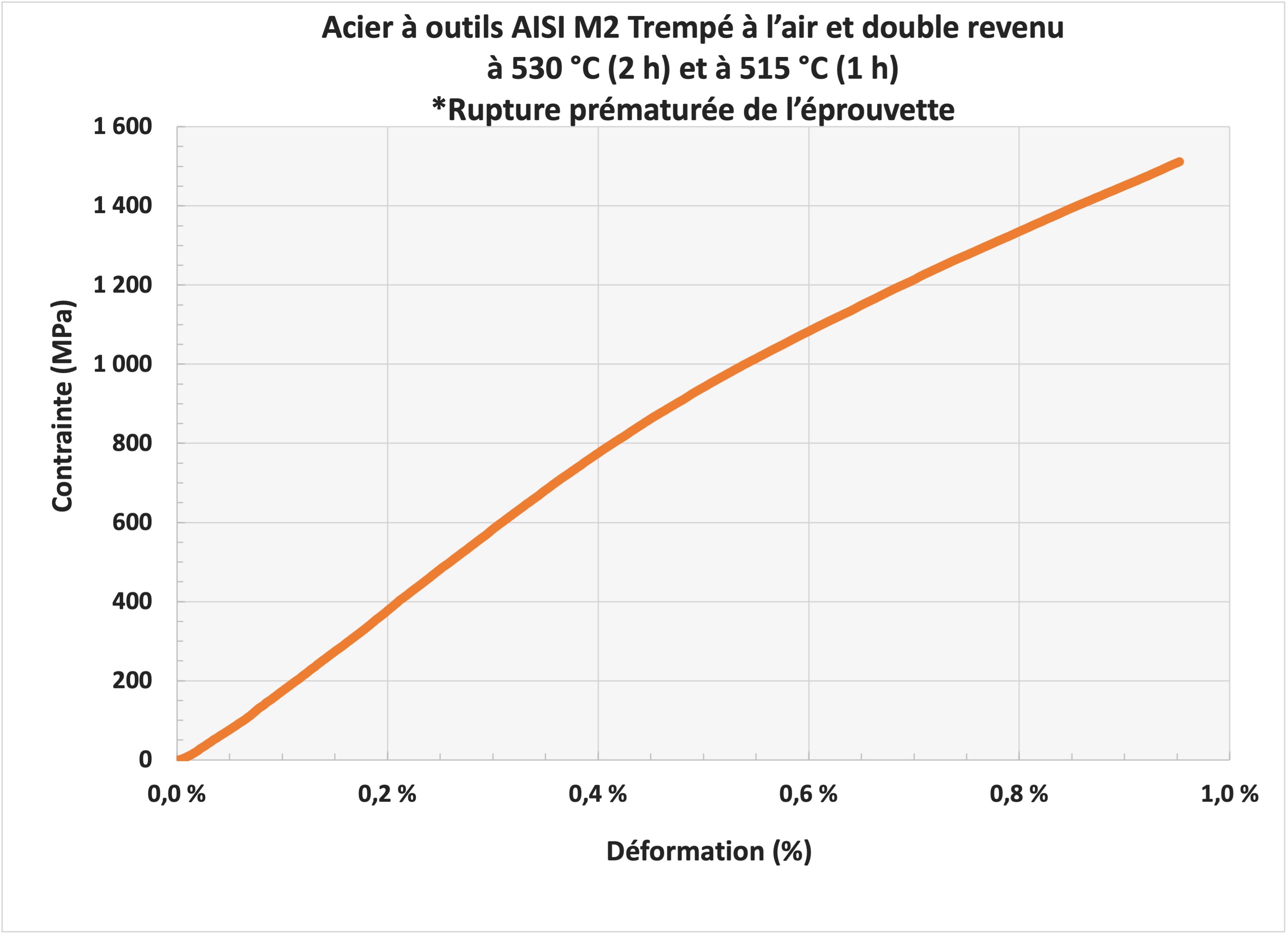